Сідельно-зчіпний пристрій, що зв'язує тягач і напівпричіп, вимагає особливого відношення в експлуатації та певного підходу в ремонті.
Підбір сідельно- зчіпного пристрою(РСУ) для нового тягача або замість зношеного необхідно здійснювати згідно з рекомендаціями та допусками конкретного автовиробника - і з цим не посперечаєшся. Так само як і з тим, що сідельний тягач та напівпричіп мають становити гармонійну систему. Її сполучною ланкою якраз і є сідло і шкворень, що входить у замок. Однак, як показує практика низки ремонтних організацій, при виборі моделі сідла для тягачів, що працюють у складних умовах, А російські до таких і відносяться, краще віддати перевагу РСУ, яка за своїми технічними характеристиками, і в тому числі максимально допустимого навантаження, перевершує той пристрій, що пропонується автовиробником у стандарті. Благо, вибір потрібного вузла, знову-таки з лінійки рекомендованих автозаводом варіантів, не становить особливих труднощів. Російським перевізникам найбільш відомі сідельно-зчіпні пристрої таких компаній, як Jost, SAF-Holland, Fontaine, Georg Fischer. У кожного з них є широка лінійка продуктів під будь-які транспортні засоби та умови експлуатації.
Саме агрегатами перерахованих вище фірм комплектують свої сідельні тягачі представники великої сімки, в яку входять Mercedes-Benz, Scania, Volvo, MAN, DAF, IVECO, Renault. Набагато рідше на тягачах трапляються сідла V.Orlandi. Однак це зовсім не означає, що їх можна списати з рахунку. на вітчизняному ринкупродукція присутня, а значить, РСУ від цієї компанії цілком може опинитися на рамі саме вашого тягача. Крім того, не виключено, що саме його вам запропонують як альтернативу зношеному. Також відзначимо, що, незважаючи на те, що кожен із виробників комерційної техніки має свого фаворита, який постачає на складальний конвеєр левову частку ССУ, бажання замовника встановити сідло іншої марки, як правило, не викликає опору з боку менеджера з продажу. У будь-якому випадку завод-виробник вантажівки купить потрібне вам сідло у свого постачальника та змонтує його на раму траку. І, нарешті, останнє: вузли, що мають схожі технічними характеристиками, мають приблизно однаковий ресурс, а також практично ідентичні за вартістю комплектних виробів та ремонтних комплектів. Вся вартісна різниця - це справа маркетингової політики і не більше.

Ті, що були в експлуатації сідла, можна придбати за 25–40% від ціни нового РСУ. При цьому залишковий ресурс вузла буде не менше чверті від початкового (ліворуч)
Проблем із кронштейнами, на які спирається плита сідла, практично не буває. Опорна їх поверхня також не зношується, оскільки вона контактує з плитою через пластикові вставки (праворуч)
Група ризику
Як показує практика, найчастіше на ремонт сідельно-зчіпного пристрою в сервіс приходять тягачі, що тягають важкі бочки великого об'єму. Найменше проблем із вузлами, що з'єднують вантажівку та класичний шторний тривісний напівпричіп. Статистику псують машини, напівпричепи яких завантажувалися з порушеннями. Наприклад, у процесі перевезення погано закріплений вантаж через трясіння зміщувався до одного з бортів причепа, внаслідок чого відбувалося одностороннє перевантаження ЗСУ. Прикінчити сідло раніше за визначений термін може і напівпричіп з несправною або неякісно відремонтованою підвіскою. При банальному розриві пневмобаллону або поломці напівресори ССУ працює з навантаженнями, близькими до граничних. Проте причини зростання зусиль на сідло можуть мати й менш явний характер. Наприклад, якщо хоч одна з осей напівпричепа виявиться не співвісною, перекошеною, то «візок» йтиме боком, а РСУ відчуватиме навантаження, скажімо так, відмінні від розрахункових. Перекошування осей може бути викликане несправною підвіскою, так і помилками, допущеними при ремонті осьового агрегату. До речі, очевидною ознакою того, що причиною виходу з ладу сідельно-зчіпного пристрою стали граничні навантаження, що йдуть від напівпричепа, є і інтенсивне зношування коліс рульової осі. До чого тут вони? Та при тому, що для того, щоб компенсувати відведення причепа від прямолінійного руху, водій змушений компенсувати сили, що діють, поворотом рульового колеса. При цьому шини кермової осі будуть йти не оптимальною траєкторією і, отже, інтенсивніше зношуватися. Примітно, що перевірка кутів установки коліс тягача, що проводиться з метою виявлення причин підвищеного зносу протектора, позитивного результату в даному випадку не дає. Усі параметри будуть у межах допустимих значень. Єдина діагностика, яка дозволить виявити наявність зазначеної вище несправності – це одночасна перевірка кутів установки всіх коліс автопоїзда.

Кожен СТО на складі має комплект самих ходових плит. У разі придбання деталей, що були в експлуатації, перевізник економить більше 60% від вартості нових компонентів. Вироблення замкового механізму може досягати кількох міліметрів. Благо, всі схильні до зносу деталі сідла виконані знімними, легко замінюються і входять в ремонтні комплекти ССУ
Причини та наслідки
Основною причиною, через яку сідельно-зчіпний пристрій вимагає до себе уваги з боку ремонтних служб, є люфт у шарнірах, що чітко фіксується при переміщенні опорної плити у вертикальній площині. Для діагностики даної несправності досить упертися брухтом у зазор між опорними плитами: основний, в замковий механізм якої входить цапфа, і опорної, через яку ССУ кріпиться до рами тягача. Навіть невеликий люфт чітко відчуватиметься на довгому важелі і безпомилково діагностуватиметься на слух. В експлуатації про наявність зазору між опорною плитою та кронштейнами, на яких вона гойдається, говорить характерне клацання, коли автопоїзд рушає з місця. Винуватцями підвищеного люфту в шарнірах в даному випадку є зношені коритоподібні прокладки, що встановлюються між основою сідла та кронштейнами, на яких воно хитається. Ці пластикові, а точніше буде сказати, виготовлені з особливого полімерного матеріалу вкладиші схильні до природного зносу. Ходімність деталей залежить не тільки від матеріалу, з якого вони виготовлені, але й від контактної площі, яку вони забезпечують. Чим вона більша, тим рівномірніше розподіляється навантаження на кожен квадратний міліметр поверхні і тим менше знос вкладишів.
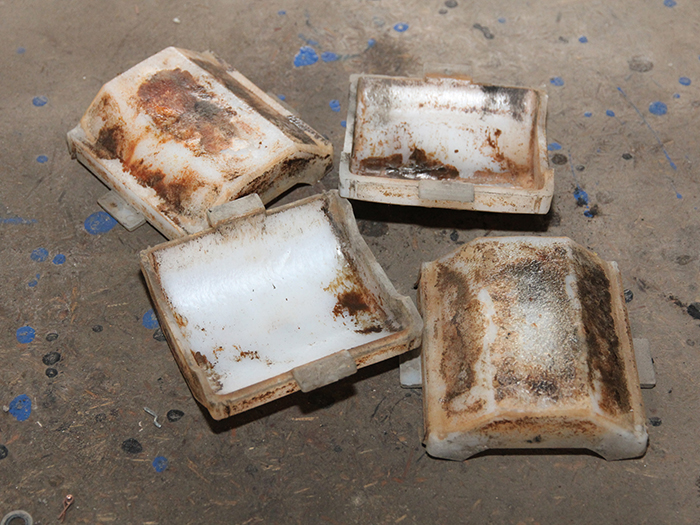
Зношені «корита» відправляємо на звалище. Жодних методів відновлення їхньої початкової геометрії немає (ліворуч). При ремонті замкового механізму обов'язково замінюємо трубопровід підведення мастила. Новий, як правило, входить у великий ремкомплект (праворуч)
Друга причина стуку – підвищений зазор у замковому механізмі РСУ. Незважаючи на те, що його величина може регулюватися, у певних рамках, зрозуміло, рано чи пізно відбудеться стирання робочих поверхонь і компенсація зазору стане недостатньою. В результаті надійне захоплення шворня буде неможливим. Наприклад, для 2,5-дюймового шкворня знос більше двох міліметрів на діаметр у ряді випадків вже критичний. Якщо не звертати уваги на удари, що йдуть від вузла, що люфтить, то в результаті цапфу може просто заклинити в замку або через ударне навантаження відбудеться послаблення кріплення, а то і зовсім відрив опорного майданчика з цапфою від причепа. Такі випадки на практиці СТО бувають, причому виявляються не рідше, ніж заклинювання шворнів. Скажімо більше. Деякі виробники напівпричепів, які постачають на російський ринок свою продукцію, мали і відгукні компанії, в ході яких виконували роботи із заміни опорних плит. Російські умови експлуатації відрізняються від європейських у гірший бік, причому чим далі від столиці на схід, тим умови гірші. Працюючи на маршрутах, що проходять через Уральський хребет, машини зношуються інтенсивніше, ніж при перевезеннях центральною частиною РФ. Взагалі, варто відзначити, що заміну плит на різних напівпричепах майстра мультибрендових станцій. технічного обслуговуваннявиробляють досить оперативно. Причому роботи виконуються як із вузлами, які приварюються до силової конструкції напівпричепа, так і з тими, що прикручуються до заставних гайок. Успішно ремонтуються й інші конструкції, у тому числі комбіновані на деяких спецпричепах. Заради справедливості зазначимо, що на заміну опорної плити та цапфи приходять напівпричепи віком від десяти років та пробігом під мільйон кілометрів.

Елементи замкового механізму можуть або продаватися окремо або входити у великий ремонтний комплект (ліворуч). Ремонтний комплект від виробника сідельно-зчіпного пристрою гарантує 100% сумісність деталей з сідлом і найвищий ресурс вузла. Ціна, зрозуміло, так само найвища (праворуч)
Однак повернемося до сідла. Нерідко ремонт РСУ може бути потрібний вже після пробігу в 25–30 тис. км. І тут велика частка ймовірності, що знос деталей вузла викликаний неправильним підбором зчіпного устрою – не враховуючи специфіки перевезень у умовах. Скажімо так, подібні проблеми з тими самими сідлами, за інших рівних умов, у європейських перевізників зустрічаються вкрай рідко. Крім того, практика говорить про те, що прив'язувати проблеми із сідлом до конкретної марки тягача також не можна. Як було зазначено вище, це буде некоректно, хоча б з тієї простої причини, що ресурс вузла і надійність його роботи залежить виключно від навантаження ССУ, що сприймається в процесі експлуатації, а також від своєчасності обслуговування. Хочемо акцентувати увагу перевізників на тому, що наявність у сідел сучасних систем автоматичного змащення, які, повинні зауважити, відмінно виконують свою основну функцію – змащення певних точок плити та шарнірів із заданою періодичністю без участі людини, проблему довговічності сідла не вирішує. Якщо вузол конструктивно слабкий для експлуатації в конкретних умовах, то скільки його не змащуй, на ресурсі РСУ це не позначиться. Крім того, не варто забувати і те, що роботу автомата так само якісно і при цьому абсолютно безкоштовно виконує водій, який при кожному розчепленні тягача з напівпричепом змащує опорну поверхню плити і замкового механізму. Саме з цієї причини переплачувати за автоматичну систему мастила РСУ немає сенсу, тим більше, що переплата ця не маленька – понад сім тисяч рублів.
У ремонт
Тепер про власне ремонт сидів. Всі РСУ, знову ж таки за практикою мультибрендових сервісних центрів, незалежно від того, хто є їх виробником, вимагають до себе уваги з боку механіків не рідше одного разу на рік або пробігу у 100 – 120 тис. км. Залежно від загального напрацювання вузла та умов його експлуатації під час проведення робіт використовується або малий, або великий ремонтний комплект. У перший входять пластикові опорні та гумові елементи, що амортизують, плюс кріплення. У другий виробник покладе ще й деталі замкового механізму та трубопровід для підведення мастила до пар тертя. Періодичність застосування комплектів становить приблизно два, або навіть три до одного. Іншими словами, повна перебирання сідла слідує за двома-трьома «профілактичними» ремонтами. Всупереч поширеній думці, ціна питання відносно не висока. Судіть самі. За часом повне перебирання сідельно-зчіпного пристрою займає, як правило, не більше двох годин. У вартісному вираженні витрати перевізника становитимуть 2700 руб. Дана цифра отримана на підставі чинної ставки нормо-години великої кількості мультибрендових сервісних центрів московського регіону, яка становить в середньому 1350 руб. Для довідки приблизно така сама сума значиться і в прайсах офіціалів, які займаються ремонтом та обслуговуванням комерційної техніки з Китаю. Тобто ціну, яку транспортник платить за ремонт РСУ, можна вважати середньозваженою та справедливою. Наприклад, у ряду офіційних дилерів європейських марок вартість нормо-години становить 1700 руб., А отже, і вартість робіт буде не менше 3400 руб.
Окремим рядком у прайсах на послуги СТО є виготовлення за індивідуальним замовленням опорних плит для регулювання висоти сідла. Цінники більшості майстерень стартують від 3500 руб. Зрозуміло, все залежить від того, яких параметрів у коригуванні висоти та положення РСУ на рамі взятої вантажівки необхідно досягти. Щоб не платити зайвого і не збільшувати час простою рухомого складу, перевізнику спершу варто ознайомитися зі стандартною пропозицією, яка має кожну станцію технічного обслуговування для конкретних моделей тягачів і сидів під них. Сервісмени, знаючи потреби основної маси клієнтів та володіючи інформацією щодо основних потреб перевізників, які адаптують свої тягачі до наявних напівпричепів, зазвичай мають на складах своїх СТО мінімальний набір плит різної висоти. Готові вироби мінімум на 40% дешевше за індивідуальні замовлення.
Щоб не помилитися з вибором потрібного ремонтного комплекту, виписуємо всі дані РСУ з таблички, закріпленої на торці сідла
Запасні частини
Ще одні граблі, куди часто наступають перевізники, – це неякісні чи контрафактні запасні частини. У прагненні заощадити транспортники нерідко купують ремонтні комплекти за підозріло низькою ціною, часом не усвідомлюючи те, що, незважаючи на особливості російського ринку, справедлива вартість запасних частин неспроможна виходити з певного цінового коридору. Скажімо більше. Ринок насичений запасними частинами, яке великі гравці тримають значення своєї накрутки фактично одному рівні. Для великих фірм це приблизно 30% заходу. Це означає, що купити якісні запасні частини дешево не вдасться за визначенням. Навіть якщо припустити, що хтось із «крупняку» вирішив розігріти ринок і встановив демпінгові розцінки на ряд продуктів, то конкуренти знайдуть спосіб дати вискочку, що зарвався, по руках. Загалом, якщо десь на ринку і відбулося скидання товару, це радше поодинокі випадки, аніж практика. Резюмуючи все сказане вище, застережемо любителів дешевизни: скупий платить двічі. До речі, здебільшого клієнту вигідно купувати запасні частини безпосередньо на СТО. Більшість великих мультибрендових сервісних станцій несе відповідальність за виконану роботу та автокомпоненти, що встановлюються, а зробити це можна тільки за умови, що запчастини мають легальне походження. Саме тому ремонтні комплекти для сідельно-зчіпних пристроїв сервісмени закуповують виключно у перевірених постачальників. Такими є великі та давно працюючі на нашому ринку торгові компанії. Оптові фірми завжди мають на своїх складах необхідні запасні частини, а також мають філії, в яких можна придбати деталі цілодобово. Отже, сервіси завжди мають можливість провести оперативний ремонт транспортного засобу клієнта та швидко випустити машину на лінію.
Малий ремонтний комплект від альтернативного виробника коштує на 45–60% дешевше від оригінального (ліворуч). У обов'язковому порядкуперевіряємо роботу замкового механізму як до, так і після ремонту. Усі зношені деталі мають бути замінені! (праворуч)
Вартість ремонтного комплекту сідельно-зчіпного пристрою, наприклад, якщо йдеться про опори сідла, в залежності від комплектації (повноти) здебільшого починається від 10 000 руб. Монтажний комплект болтів, що купується окремо від ремонтного комплекту, обійдеться в 1,5-2 тис. руб. Зауважимо, що металовироби виготовляються з певного сплаву і проходять строго певну термічну обробку, яка задає кріпилю необхідну міцність. На різьблення болтів наноситься спеціальний фіксуючий склад, який запобігає самовідвертанню кріплення в процесі експлуатації автопоїзда. Якщо такий склад не завдано, то це необхідно зробити безпосередньо перед збиранням. Якщо сідло має антифрикційні накладки, то комплект на заміну зношених потягне від 12 000 до 18 000 руб. Зрозуміло, кріплення, необхідне їх фіксації на чавунної плиті, буде дбайливо укладений виробником в упаковку. Зрозуміло, вартість накладок залежить від матеріалу, з якого вони виготовлені. Чи варто економити та купувати дешевші запасні частини – питання для більшості російських перевізників, які вже неодноразово обпалювалися на «сирих» деталях, закрите. У останні рокипростежується чітка тенденція вибору транспортниками нехай дорогих, але якісніших автокомпонентів, які мають кращу ходимість. Що стосується клину замку сідла, то в залежності від моделі РСУ дані деталі оцінюються від 2 до 7 тис. руб. Найдорожче коштують балансири сідла, деякі моделі яких просять 50 000 крб. і більше.
© Jost
Сідельно-ланцюговий пристрій, будучи основним компонентом, що з'єднує тягачі напівпричіп, удосконалюється відповідно до тенденцій світового автобудування. Судячи з новинок у цій галузі, активне впровадження електроніки та автоматики вже дозволило суттєво підвищити безпеку, спростити обслуговування, а також скоротити час, необхідний для зчеплення-розчеплення.
Можна припустити, що одне з перших седельно-
зчіпних пристроїв автопоїзда з'явилося наприкінці ХІХ століття. Саме тоді на відомій автомобільному світу фірмі De Dion-Bouton був придуманий напівпричіп, який частину вертикального навантаження від власної маси і маси вантажу, що перевозився, передавав на раму тягача - трицикла на паровому ходу.
У ті далекі роки, зрозуміло, ніхто й не припускав, що через сторіччя основна ланка зчіпки стане такою складною: механіка вступить у союз із пневматикою і навіть електронікою. Сьогодні тенденції світового автомобілебудування, крім гарантованої надійності, вимагають від цього вузла підвищеної зносостійкості та зручності в обслуговуванні.
© Jost
Конструкція
Сучасний сідельно-зчіпний пристрій (ССУ) включає ряд важливих компонентів. Це, перш за все, опорна плита, роз'ємно-зчіпний механізм, що сприймає разом з пристроєм кріплення тягові та гальмівні зусилля, а також вузол забезпечення гнучкості. Зчіпна пара утворюється після того, як шкворень, закріплений на напівпричепі, увійде в проріз опорної плити і зафіксується замковими деталями шарнірно закріпленими на пальцях.
В даний час застосовується два види роз'ємно-зчіпних механізмів: одно- та двозахоплювальні. Перший поширений переважно серед продукції європейських виробників, таких як Jost, Georg Fischer, Saf Holland, а другий зустрічається в продукції вітчизняного автомобілебудування (приклад - сідельний тягач ЗІЛ-442160). Їх принципова відмінність полягає в тому, що в двозахоплювальному механізмі тягові зусилля сприймаються лише захопленнями і сполученими з ними пальцями, а в однозахоплюючому передаються ще й на масивний запірний кулак, при цьому відповідальна деталь схильна лише до стискаючих зусиль. Як наслідок – додаткова надійність та безпека конструкції.
© Jost
Типи, основні розміри та технічні вимоги, які пред'являються до РСУ, регламентуються міжнародними та вітчизняними стандартами. Так, згідно з нормативними документами, є два різновиди виробів. Перша, тип 50, налаштована під діаметр зчіпного шворня 50,8 мм (2”), а друга, тип 90 - під 89 мм (3,5”). Застосування тієї чи іншої групи залежить від вертикального навантаження, а також повної маси автопоїзда та напівпричепа. Наприклад, тип 50 використовується, якщо повна масанапівпричепа не виходить за межі 55 т або вертикальне навантаження не перевищує 20 т, при більшій масі застосовують тип 90. До речі, у деяких виробах закордонних виробників передбачена можливість швидкого переналагодження з одного типу шкворня на інший. Серед інших важливих параметрів, що впливають на вибір ССУ, можна назвати конструктивну висоту, що впливає на вертикальний габарит, і наведене навантаження (т. зв. значення D, що вимірюється в кН), яка відображає характеристики вузла міцності.
Для гнучкості зчеплення ССУ повинно мати три ступені свободи, що забезпечують поворот напівпричепа навколо вертикальної осі шворня, хитання в поздовжній площині вперед і назад (кут не менше 11°), а також поперечний нахил вліво та вправо (не більше 3°). Два з цих умов виконуються завдяки наявності поперечної осі та «м'якості» у точках кріплення опорної плити. Разом з тим виготовляються спеціальні сідельні пристрої зі збільшеним максимальним кутом поперечного нахилу. Розширення свободи досягається завдяки наявності додаткової поздовжньої осі. Виходить така собі подоба карданного шарніра, який забезпечує вже інші можливості. Наприклад, у сідельному пристрої SK-HD 38.36 G максимальний кут нахилу в ліву та праву сторону досягає 7°. Подібні технічні рішення зазвичай використовуються для автопоїздів, що експлуатуються на бездоріжжі, або транспортних засобів, призначених для перевезення важких вантажів, коли існує можливість передачі на раму значних скручувальних моментів. А суттєвим недоліком таких систем є зниження стійкості автопоїзда під час руху, тому для автопоїздів, що виїжджають на дорогу з якісним покриттям, хитання напівпричепа навколо осі обмежується спеціальними упорами механізмом. У складніших конструкціях застосовуються стабілізатори.
© Jost
У всьому світі виробники вантажівок намагаються зробити основні вузли автомобілів легшими, щоб заощаджувати паливо та підвищити корисне навантаження. Звичайно, не залишаються поза увагою питання зниження маси сідельно-зчіпних пристроїв.
Один із шляхів до цього – використання нових матеріалів та технологій. Взяти, наприклад, опорні плити. Вони бувають литими та штампованими. У першому випадку матеріалом є кулястий графіт, а в другому - міцна сталь. Але вибір сьогодення цими варіантами не обмежений. Так, компанія SAF-Holland у співпраці з фірмою Alcoa нещодавно випустила до серії РСУ моделі FWAL-E з опорною плитою з алюмінієвого сплаву. Легкий виріб призначений для встановлення на тягачі з максимальним навантаженням на зчіпний пристрій 20 т та показником D, рівним 150 кH. Зниження ваги в порівнянні зі звичайною конструкцією становить приблизно 30 кг, а також завдяки полімерній накладці, закріпленій на опорній плиті, виріб протягом усього терміну експлуатації не вимагає мастила.
© Jost
До речі, ні для кого не секрет, що технологія мастила безпосередньо пов'язана з питаннями екології. Розробляючи новинки, конструктори ніколи не залишали осторонь таку тему, як попадання в навколишнє середовищенадлишків мастильних матеріалів, у тому числі й від таких «рясно обслуговуваних» вузлів, як зчіпні пристрої. Тому там, де без мастила не обійтися, використовуються механізми автоматичного дозування. Наприклад, для високонавантажених ССУ серії JSK 42 компанія Jost пропонує новинку – Lube Tronic-5 Point. Запас матеріалу зберігається у спеціальному картриджі і з певними інтервалами подається в кілька точок, розташованих на опорній плиті та у замковому пристрої. За точністю дозування слідкує електроніка. Передбачено кілька режимів роботи: для довгих дистанцій з рідкісними розчіпками або важких умов з високими навантаженнями. Ємності стандартного картриджа вистачає на мастило протягом 12 місяців.
З пультом у кабіні
© Jost
Серед тенденцій, що виявляються в Останнім часомможна виділити новинки, пов'язані з механізацією процесу зчеплення-розчеплення автопоїзда та електронним контролем стану РСУ. Як одне з підтверджень назвемо сенсорну систему безпеки RECOSS, яку пропонує компанія Georg Fischer для дооснащення сідельно-зчіпних пристроїв SK-S 36.20. Система включає три сенсори, розташованих безпосередньо в РСУ, і сигналізатора, розміщеного на робочому місці водія. Ця «трійка» здатна не тільки безперервно контролювати правильність взаємного положення замкових деталей, але й вимірювати відстань між плитою напівпричепа та сідлом тягача, забезпечуючи цим правильність підведення та зчіпки. Наприклад, якщо в процесі з'єднання ланок автопоїзда сідло і шворень будуть перебувати на різній висоті, водій почує звуковий сигнал.
Аналогічна система є і в арсеналі компанії Jost, причому як нова опція фірма пропонує бездротове з'єднання з сигналізатором по радіоканалу. Це значно полегшує монтаж системи та дає можливість швидкого перенесення кабінного блоку у зручніше для оператора місце. Функціональні можливості такої системи можна підняти на більш високий рівеньза рахунок встановлення пневмоприводу, який автоматично розблокує зчіпний пристрій перед розчепленням (система Jost SKS).
© Jost
Ще більш «просунутою» є електронна системакомфортного зчеплення Jost KKS. Вона не тільки виключає ручне роз'єднання замкового механізму зі шворнем у момент розчеплення, а й автоматизує підключення пневмоелектричних комунікацій та вертикальне переміщення опор напівпричепа. На минулорічній виставці комерційного транспорту в Ганновері нам вдалося ознайомитись із цією системою, оглянувши фірмовий автопоїзд.
© Jost
Електронна частина нового зчіпного вузла в цілому аналогічна сенсорним системам безпеки, що вже добре зарекомендували себе: два датчики контролюють захоплення, а третій - висоту сідла в момент зчіпки. Механізм пневматичної розчіпки, що знаходиться під опорною плитою (укомплектований про всяк випадок звичним важелем) також конструктивно близький до вже відомих варіантів автоматизованих сідел. А от щодо універсального пневмоелектричного роз'єму, аналогів йому поки що не існує. Про наявність такої системи в зчіпці можна здогадатися по конструкції шкворневого вузла, який частково нагадує пристрій напівпричепа, що стежить, з керованими осями.
Представлений варіант роз'єму включає два пневматичних і двадцять два електричних контакту (п'ятнадцять з них служать для з'єднання ланцюгів світлової сигналізації і освітлення, а сім залишаються відносяться до системі ABS). Як опція передбачена можливість додаткового розширення для кабелю електронної гальмівної системи TEBS, камери заднього виду та електроприводу механізму опорного пристрою. Автоматизована вилка тягача змонтована під плитою сідла і, таким чином, додатково захищена від бруду та вогкості. контактна групаприкрита мініатюрним кожухом. Стикувальний вузол напівпричепа, своєю чергою, є поворотний клин, шарнірно закріплений у виточці біля основи шворня. Усередині клина знаходиться відповідна частина роз'єму - розетка. Під'єднані до неї кабелі та трубопроводи не повинні перешкоджати вільному повороту клина щодо шворня, тому у складі KKS є пристрій, який постійно регулює їх довжину.
© Jost
У процесі зчеплення клин напівпричепа фіксується в гирлі опорної плити подібно до збирання фрагмента в дитячій мозаїці. Далі, отримавши повідомлення про повну фіксацію шкворня в захопленні, автоматика переміщує вилку у бік розетки, і пневмоелектричне з'єднання замикається. Тривалість процесу з'єднання з урахуванням спрацьовування всіх механізмів та остаточного контролю не перевищує 3 секунди. Після цього водію залишається, натиснувши відповідну клавішу пульта керування, підняти опорні пристрої та підготуватися до руху. У процесі роботи за кермом також гарантовано постійний моніторинг та негайне повідомлення про будь-які неполадки.
До речі, універсальність Jost KKS дозволяє з'єднувати ланки автопоїзда в будь-яких варіантах, наприклад, модернізований тягач і звичайний напівпричіп або навпаки - звичайний тягач і напівпричіп з новим шкворневим вузлом. При цьому підключення електричних кабелів та повітряних шлангів буде виконано за стандартною схемою.
Залишається додати, що за інформацією виробника новинка з'явиться у широкому продажу після завершення експлуатаційних випробувань. Однак про точні терміни та приблизну ціну пристрою поки не повідомляється.
І ще. Судячи з тенденцій на ринку автокомплектуючих, цей напрямок надалі розвиватиметься. Подібні розробки незабаром з'являться і в асортименті відомих виробників.
Доатегорія:
Автобуси та спеціальні автомобілі
Зчіпний пристрій сідельного тягача
Для з'єднання тягача та напівпричепа застосовують опорно-зчіпний напівавтоматичний пристрій. Основою опорно-зчіпного пристрою сідельного тягача служить укріплена болтами на лонжеронах рами плита, яка з'єднана з сідлом 6 з використанням кронштейна та осі балансиру. Таким чином, зчіпний пристрій має дві осі, навколо яких сідло може хитатися як у поздовжній, так і поперечній площинах. Вісь встановлена у двох кронштейнах, пригорнутих до плити болтами. Відхилення сідла разом із балансиром щодо цієї осі обмежено двома обмежувачами бічного найлону. Залежно від положення останніх кути відхилення сідла можуть дорівнювати 15, 8 і 0°. На закріплених у сідлі осях встановлено два захвати. У передній частині напівпричепа розміщені дві опори та шворень.
Мал. 1. Сідельно-зчіпний пристрій: а - вид збоку; б – вид знизу; 1 - драбини; 2 – плита; 3 – кронштейн кріплення сідла до плити; 4 – вісь балансиру; 5 – запобіжник; 6 – сідло; 7 - обмежувач бічного нахилу сідла; 8 - санки сідельного пристрою; 9 - лонжерон рами; 10 - розпірка лонжерону; 11 – тримач плити; 12 і 16 - масляки; 13 – кронштейн сідла; 14 - вісь захоплення; 15 – захоплення; 17 - вісь сідла; 18 – важіль управління; 19 - запірний кулак зчіпного механізму; 20 - спрямовуюча вісь кулака; 21 - пружина; 22 - вісь; 23 - клямка запірного кулака; 24 - штифт захвату; 25 - пружина засувки
Для зчеплення напівпричепа з тягачом передню частину напівпричепа розташовують на такій висоті, коли передня кромка його опорного листа лягає на сідло. Електричні дроти та з'єднувальний шланг гальмівної системи підвішують на гачок переднього борту напівпричепа, щоб вони не заважали зчіпці. Обмежувачі бічного нахилу сідла відсувають назад і стопорять у цьому положенні болтами. Запобіжник саморозчіпки повертають убік. Якщо захоплення не розкрито, то важіль управління переводять вперед у положення, що фіксується засувкою запірного кулака. Під час зчеплення шворень напівпричепа розводить убік передні кінці захватів, а пружина вводить запірний кулак зчіпного механізму між задніми кінцями захватів і замикає шворень між ними. При цьому важіль перетворюється на заднє положення, і запобіжник опускається. Для полегшення зчіпки виїмка в сідлі зроблена, а сідло встановлено на осі з нахилом назад.
Після зчеплення з'єднують пневматичні та електричні системи тягача та напівпричепа. Катки напівпричепа піднімають, опускають гальмо стоянки, і тягач з напівпричепом готовий до руху.
Для розчеплення тягача з напівпричепом у загальмованого гальмом стоянки напівпричепа опускають опорні катки до упору в поверхню дороги або в іншу опору. Потім закривають роз'єднувальні крани і роз'єднують сполучні головки пневматичного гальмівного приводу до причепа та електропроводу. Підвішують шланги та дроти на гачок переднього борту напівпричепа, щоб вони не заважали розчіпці. Запобіжник відводять убік. У напівпричепа, зчепленого з тягачом, шворень затиснутий між захватами 15 зчіпного пристрою тягача, тому кулак, що замикає захоплення, відводять вперед важелем управління розчіпкою. Запірний кулак утримується у відведеному положенні клямкою, що упирається в його заплечики. Засувку щодо осі повертає пружина.